Machines
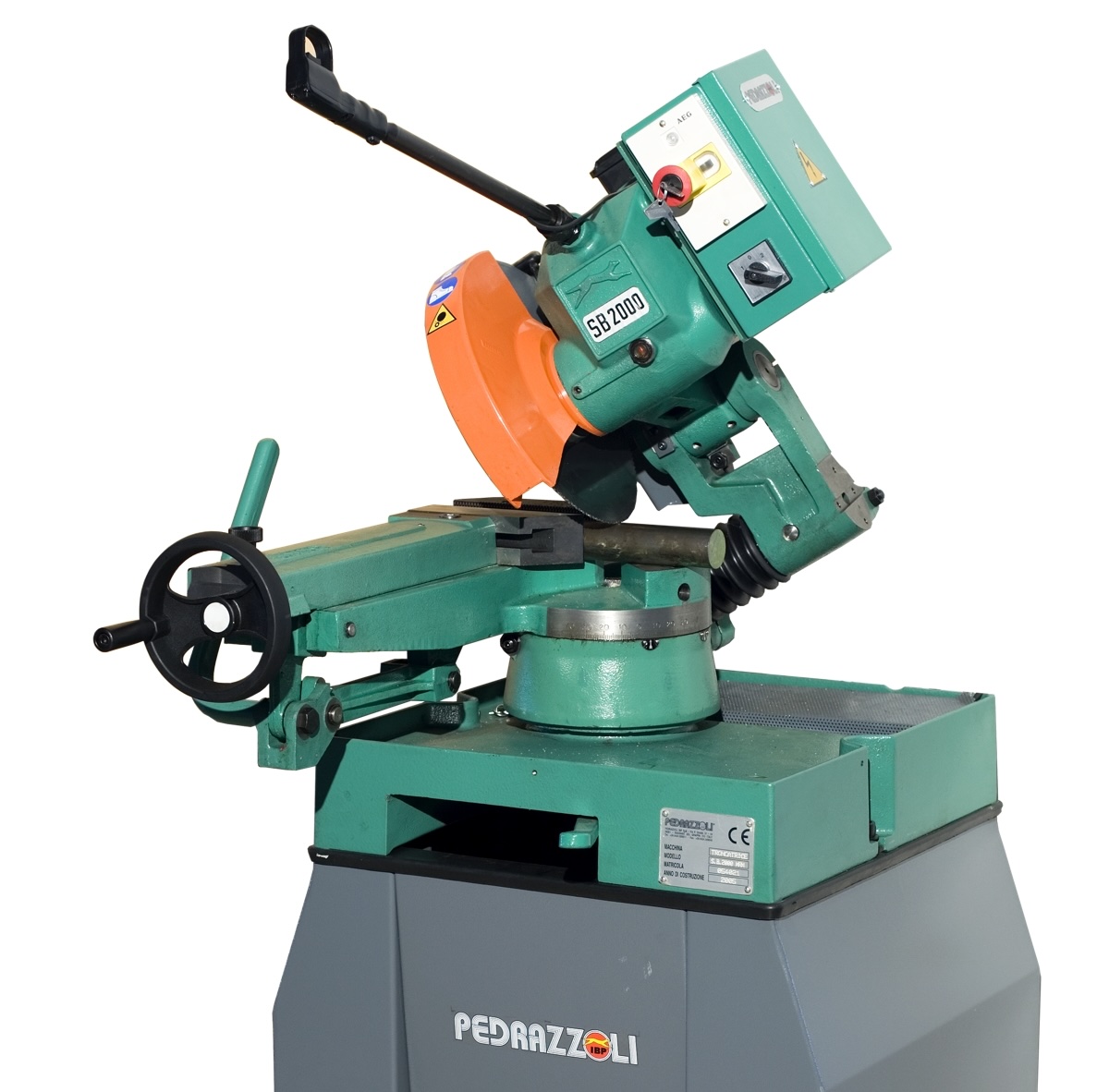
Pedrazzoli Circular Saws
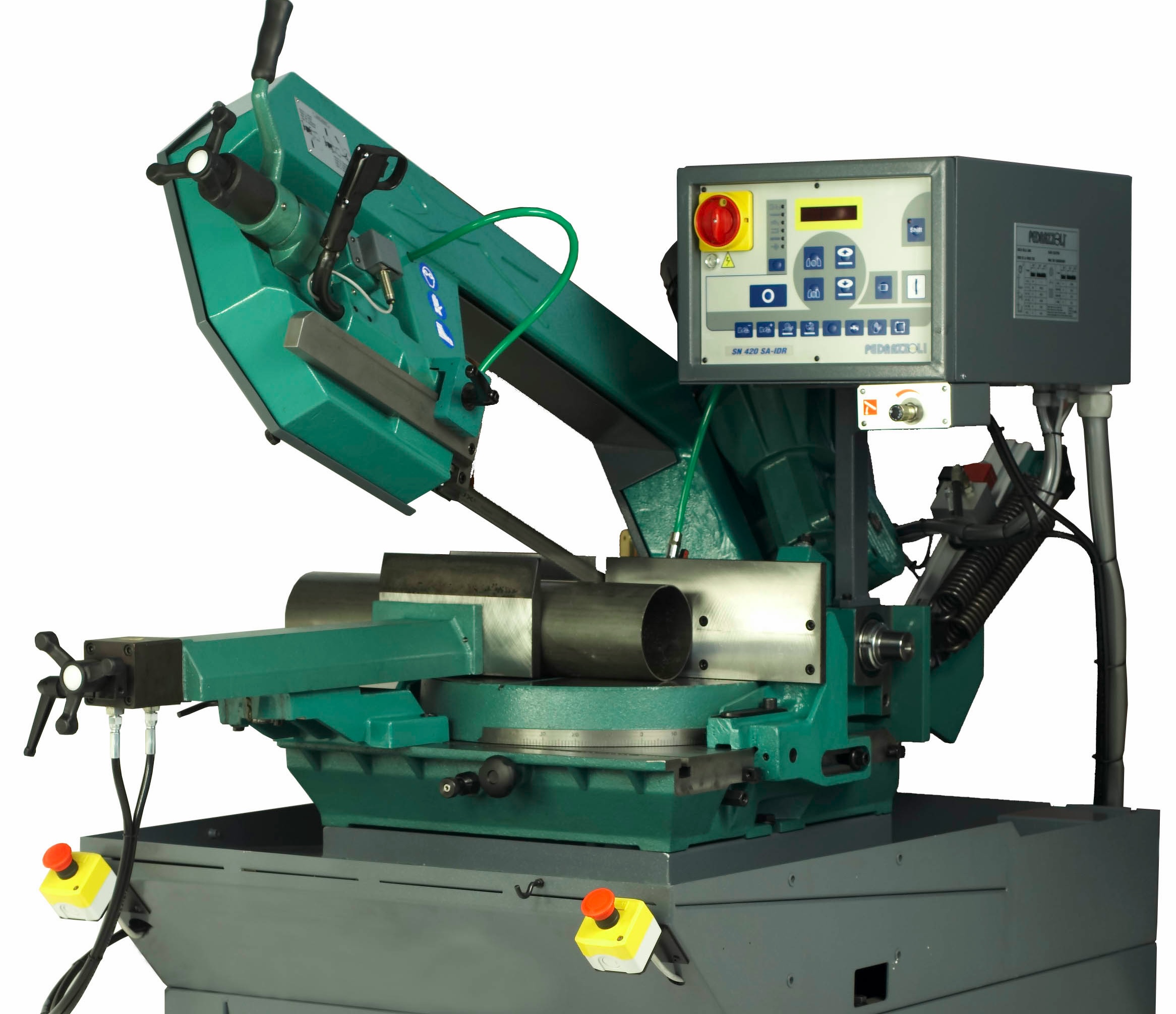
50 years of sawing experience sawing metal up to 25 tonnes in finished, part finished, rolled, cast, forged or mill form. Supplier of quality bandsaw blades, band saw machines, circular saw blades machines.
CONTACT US50 years of sawing experience sawing metal up to 25 tonnes in finished, part finished, rolled, cast, forged or mill form. Supplier of quality bandsaw blades, band saw machines, circular saw blades machines.
CONTACT US50 years of sawing experience sawing metal up to 25 tonnes in finished, part finished, rolled, cast, forged or mill form. Supplier of quality bandsaw blades, band saw machines, circular saw blades machines.
CONTACT US50 years of sawing experience sawing metal up to 25 tonnes in finished, part finished, rolled, cast, forged or mill form. Supplier of quality bandsaw blades, band saw machines, circular saw blades machines.
CONTACT US